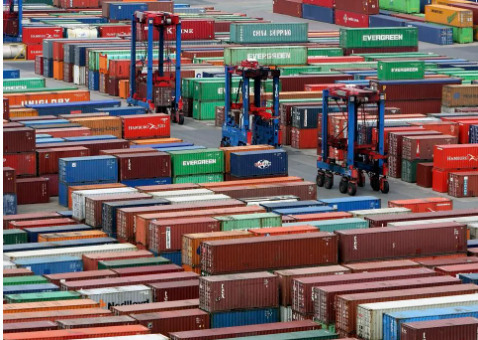
When it comes to managing your organization’s supply chain, two of the most common terms you’ll hear tossed around are “logistics” and “supply chain management.” Many people assume that these are interchangeable words that describe the same thing …
But they’re wrong.
While supply chain management and logistics certainly have similarities, they are actually two different things. By understanding the difference between them and how they relate, you can be better equipped to keep your own supply chain running smoothly.
So, What’s the Difference?
According to the Council of Supply Chain Management Professionals (CSCMP), supply chain management “encompasses the planning and management of all activities involved in sourcing and procurement, conversion, and all logistics management activities.”
The words “all activities” are especially important. This means that true supply chain management is heavy on collaboration with suppliers, third party service providers and channel partners. It looks at the whole supply chain process from start to finish, both internally and externally.
As Carmit Glik, CEO of Ship4wd, a digital freight forwarding platform for SMBs, explains:
“Logistics is a part of the supply chain — but it isn’t the supply chain itself. […] Logistics, on the other hand, is the process of planning, implementing and controlling the flow and storage of goods. Hence, it is mainly about movement and transportation of products as well as management of inventory and warehousing. Logistics activities include transportation management, inventory management, order fulfillment, packaging and distribution of goods and services. The goal of logistics is to ensure that the right product will be in the right place at the right time in the most cost-efficient way based on customers’ needs.”
So, while logistics and supply chain management are closely related, it’s not because they are the same thing. In reality, it’s because logistics is a core component of successful supply chain management.
But logistics isn’t the be-all end-all of your supply chain. True supply chain management encompasses several additional activities, ultimately covering the entire lifecycle of any given product — from the moment you start sourcing to when it is sold.
Embracing the Big-Picture View of Supply Chain Management
Successful supply chain management doesn’t undercut the importance of logistics — few things are more important! But it also recognizes that logistics are one piece of a bigger whole. In fact, Michigan State University notes that innovation and product development, purchasing and sourcing, manufacturing and operations, customer service and global deployment also fall under the umbrella of supply chain management.
Most notably, Michigan State describes supply chain management as something that “involves collaboration between firms to connect suppliers, customers and other partners as a means of boosting efficiency and producing value for the end consumer. […] Supply chain management activities [are] strategic decisions, and set up ‘the operational framework within which logistics is performed.’”
Note the key word of collaboration when describing supply chain management. With so many interrelated activities taking place with the goal of providing value for the end consumer, collaborative partnerships are essential for making this happen.
Suppliers, retailers, manufacturers and wholesalers must work in close collaboration to ensure that everything runs efficiently at all stages — from product development to logistics to customer service. If any one partner fails to hold up their end of the agreement and their aspect of the supply chain doesn’t live up to the expectations of the end consumer, it hurts customer acquisition and retention, which in the long run will damage the reputation and profitability of every organization involved in the supply chain.
When organizations are committed to strong partnerships and oversight of each facet of the supply chain, supply chain management can become a significant competitive advantage that allows them to better manage costs while consistently delivering quality results to their consumers. Notably, 79% of organizations with “high-performing” supply chains experience above average revenue growth.
Understanding Logistics as Part of Supply Chain Management
Of course, none of this is meant to downplay the importance of logistics — particularly when there are several types of logistics that businesses must be mindful of.
First are inbound logistics, which entail a manufacturer receiving raw materials (supplies) from an external partner so they can create their products. Then there are outbound logistics, or moving and storing products from the manufacturer to the end customer.
Finally, reverse logistics covers what happens after a product is delivered to a customer — such as those instances when a customer returns a product to the retailer for exchange, repair or other reasons.
Coordinating shipping, packaging and transportation can be extremely complicated on its own, which is why so many organizations use third party logistics (3PL) providers to handle these matters for them. By working with a 3PL, organizations can ensure efficient logistics outcomes that meet the needs and requirements of the end customer, whether that customer is a warehouse or an everyday consumer.
It’s important to recognize that these activities only fall under one specific area: moving inventory and raw materials to the desired location, be it a warehouse, retailer or end consumer. If it isn’t directly related to moving goods from one place to another, it’s not logistics.
Understand These Concepts to Improve Your Own Supply Chain Outcomes
It’s easy to mismanage your business when so many industry leaders talk about logistics and supply chain management as being essentially the same thing. But when you understand that logistics is simply one important facet of supply chain management, you can adopt a macro view of the supply chain — one that ultimately better serves your business from start to finish.
When you adopt a more holistic understanding of the supply chain and all of the activities that are involved in it, you will be better equipped to identify the right opportunities for collaboration and develop a big-picture strategy that delivers the results your customers deserve.
Source: Forbes