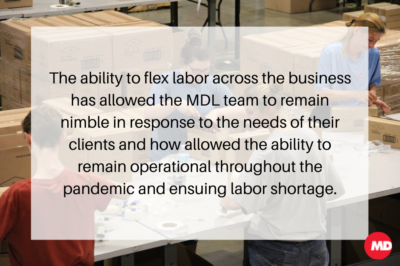
Background
There are a myriad of things that could happen to disrupt the flow of the supply chain. The COVID-19 pandemic was one of those disruptions that transformed the world and forever altered the way in which supply chain’s, everywhere, operate. One of the many disruptions that the supply chain experienced during this time was a shortage of available labor. Prior to the COVID-19 pandemic, due in part to the growing demand for ecommerce, the supply chain was already experiencing a shortage of readily available labor. The shortage was exacerbated in the ensuing days of the pandemic as more and more consumers moved to ecommerce channels for all of their shopping needs. This shift, coupled with the need to take time off to care for family members due to illness of the closing of schools, created a labor challenge for 3PL providers and supply chains everywhere.
Challenge
In the early days of the pandemic, third party logistics providers were tasked with finding a solution to respond to both an influx of orders and a decreased labor pool, without compromising on the level of service, the consumer has come to expect.
Solution
MD Logistics operates as a 3PL within two very distinct and separate industries, Life Sciences and Pharmaceuticals and Retail and Consumer Goods. These two industries have their own set of handling requirements and quality controls in place to ensure the integrity of the product. Because these two industries are so distinctly different, traditionally, the best way to deliver a lasting customer experience would be to have separate, highly specialized teams operating within each industry. While this worked for many 3PL’s, including the team at MD Logistics, in the past, the events of the last year have proven a need for greater flexibility across all areas of the supply chain.
Throughout the pandemic, as some areas of the business slowed, others got busier. This created an opportunity to alleviate a portion of the labor shortage we were experiencing by flexing labor across the business. The solution is made possible by keeping these elements in mind:
Collaboration. Cross collaboration between the facilities within our four-facility Plainfield, Indiana campus ensures that all areas are properly staffed, flexing team members where needed. Both of the industries in which MDL operates, have a seasonality to their business. Cross collaboration is key to making sure all needs of the business are met throughout the year.
Open Communication. Consistent open channels of communication ensure that as additional staffing needs arise, they can be met and fulfilled. This allows our management team to be aware of events all across the business.
Company Culture. The culture at MD Logistics supports a ‘can do’ attitude and is very much a team environment. By creating an environment which supports assistance within the organization, produces a team oriented group of individuals all with a willingness to assist where needed.
Technology. Utilizing the same WMS across the MDL organization creates a more seamless transition of personnel from one operation to another. Understanding how product moves through the WMS, and in turn through the warehouse, makes it easier to move between the two industry verticals in which MD Logistics operates.
Training. Training is a critical part to being both successful as a 3PL and delivering an exceptional customer experience. By creating a flexible labor environment you have to, in turn, create a training program which covers all aspects of your business. For MD Logistics, it’s making sure that team members in our retail and consumer goods environment are able to work in our life sciences and pharmaceuticals warehouses and vice versa.
Results
The ability to flex labor across the business has allowed the MDL team to remain nimble in response to the needs of their clients and how allowed the ability to remain operational throughout the pandemic and ensuing labor shortage. The elements needed for a flexible labor environment have also allowed our team members to lend their expertise in a different area of the business from where they work. This cross collaboration brings new ideas to better respond to the challenges in our customer’s supply chains.