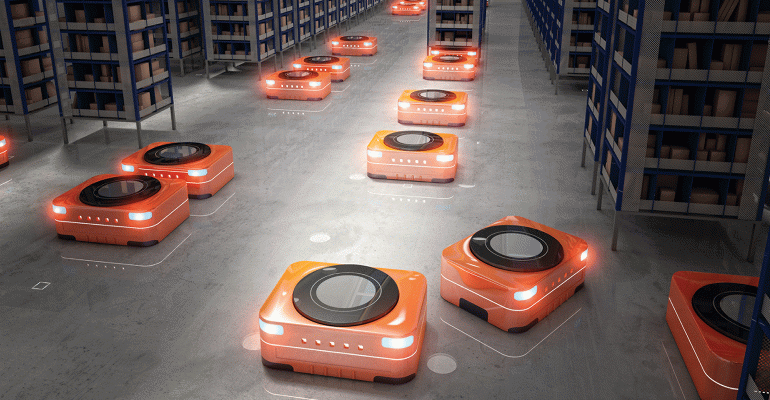
Robots and AGV’s are already solving picking and sorting challenges in DCs, and they’re just getting started.
Customer expectations are changing as new sales outlets are being used. With the application of social media, omni-channel and e-commerce customers now have more price options, selections, delivery methods and shopping experiences. The ability of a business to keep the customer satisfied greatly depends on fulfillment capabilities.
Progressive businesses have realized the critical nature an operations strategy has on designing a working supply chain. Combining distribution and fulfillment operations into a single facility has become the base of the supply chain network, as they allow a single location to stock a vast number of products and service multiple channels.
Since order fulfillment first became more automated for catalog sales back in the 1980s, its main justification has been to remove the travel time and distance by staff involved in processing orders, while improving accuracy and order fulfillment cycle times. With the rapid growth of online ordering and e-commerce in the past decade, the opportunity for automation of order fulfillment has hit new heights.
Much has changed since then with both customer expectations and technology. The elimination of walk and travel time, while still a key component in evaluating automated solutions, is not necessarily the driving criteria. Today’s distribution centers (DCs) and fulfillment centers (FCs) need to add flexibility, scalability and reduced reliance on temporary or unreliable labor pools to meet their operational requirements.
With the recent evolution of goods-to-person and robotic order fulfillment technology, your operation may be in a better position to incorporate these automated solutions now than in the past. In many cases, the implementation of automation to reduce or improve the leverage of labor is a key driver now. In addition, many new automated solutions can be obtained at a lower capital investment and be expanded as needed, which reduces the initial investment and improves the overall return on investment.
There is a new world of automation options on the market, from robots roaming a DC/FC, to highly automated conveyors and equipment that assist staff with faster fulfillment processes. Traditionally, products are moved around a DC/FC using humans, human-operated machines, or conveyor system that have been around for decades. Although robots have been around for many years, until recently, they have been very limited in capability, functionality and performance in the world of DC/FC.
Today, there are many types of robots available to help with DC/FC operation tasks. These robots can assist with loading, unloading, sorting, picking, transportation, storage, delivery and audits. Robots helping with these tasks come in all shapes and sizes. They also use different forms of navigation tools such as rail, wire-guided, labels, magnet tape, laser, vision, geo-guidance and others. This article focuses on the robots that assist with the picking and sorting of items that go into a unique order.
Picking
As e-commerce continues to grow and the replenishment to stores moves to less than case quantities, the trend away from case or bulk movement handling toward single SKUs and piecemeal items expands along with it. Anyone who has gone to a material handling trade show or has read industry journals are aware of goods-to-person systems that have evolved over the past decade. Many will remember the introduction of autonomous robotic solutions such as Amazon Robotics (formerly Kiva). In addition, other solutions were developed to effectively compete in this space.
These types of goods-to-person systems have taken the form of large, forward pick, racked systems that use robotic vehicles and carriers to bring cases and totes of goods to stations and then return the item container back into storage. At each station, an operator is then directed on the quantity of each item to pick and which order or orders need the items. The pick and placement of items is directed and the operator works at a highly effective rate due to no travel, system direction, and the fast introduction and removal of goods and orders to process.
There are many versions of the goods-to-person systems available on the market, including systems from such companies as AutoStore, Dematic, OPEX and SSI Schaefer. These systems operate with the same basic process described above.
AutoStore has a unique, high density storage design with the robotic vehicles operating on a grid above the storage system, which minimizes space and eliminates all aisles while performing the putaway, retrieve and movement functions. It is a new and different design that is gaining user acceptance. In fact, it was recently announced that Dematic will be an authorized distributor of AutoStore, while it also continues to sell its own proprietary goods-to-person Multi-Shuttle system.
In recent years, there has evolved a trend of picking enhanced by robotic equipment and systems that do not require a large infrastructure and high capital investment, such as the typical goods-to-person system. Locus Robotics is one such solution and has engineered a new approach to less-than-case fulfillment operations. These are autonomous mobile robots, called LocusBots, that work safely alongside human employees to deliver higher e-commerce and less-than-case fulfillment throughput and efficiency. LocusBots automatically detect a wide range of worker’s languages, changing instantly as they interact with each worker to help speed workflow and minimize errors. The integrated scanner confirms the item and ensures near 100% accurate pick and put operations.
Another evolving trend is using robotic machines to perform the pick process. These systems can detect, reach out, grasp and place into a receptacle items to fulfill an order. RightHand Robotics, for instance, provides end-to-end solutions designed to reduce the cost of e-commerce order fulfillment of electronics, apparel, grocery, pharmaceuticals, and other industries. The core competency of the RightPick solution is picking “pieces” or individual items. Unlike traditional factory robots, RightPick handles thousands of different items using a machine learning backend coupled with a sensorized robot hand that works in concert with all industry-leading robotic arms.
Sortation
Currently, there are not many applications of robots doing item sortation in the United States. A technology that has been around for decades is the automated guided vehicle (AGV). An AGV is a portable robot that follows markers or wires on the floor, or uses vision, magnets, or lasers for navigation. AGVs have been used for case, pallet, bulk, or specialized container movement for many years across a wide range of industries and applications.
A recent example of an AGV used in sortation is t-Sort, a new material handling system created by Lab Z that has applications for both unit and parcel sortation. It performs much like a traditional automated sortation system, such as a tilt tray or crossbelt sorter. However, it uses completely independent robots, which are the equivalent of having a tilt tray with no rail. They can go to any divert and induction station autonomously along the shortest path. Robots, chutes or receiving receptacles, and induction stations can be added modularly at any time with no interruption to operations. t-Sort is a means of automated order fulfillment for units to complete an order and parcel shipping operations, allowing for better planning, implementation, controls efficiency, flow of goods and customer service. The system is flexible and can be deployed in any size DC/FC.
Another example, Sure Sort, is a scalable, configurable, small-item sorting system. Designed and manufactured by OPEX Corp., Sure Sort is a robotic item sorter that handles complex variables and delivers a variety of single items to their final location in a single pass. Its compact array of sort locations can be scaled, sized and customized as well. It delivers by reducing the number of touches, transfers and conveyors required to run existing sorters. The system can handle a range of sizes, different packaging and varied orientation of an item. It automatically reads a barcode and delivers each item in a single pass to a designated order consolidation point. It is suitable for small businesses looking for a cost-effective entry into warehouse automation as well as large fulfillment operations looking to streamline their process.
The Economics of Robotics
Supply chain DC/FC performance is very sensitive to changes in business strategy and operating environments. Some of these changes include market changes, acquisitions, new products or packaging, new sales channels, and growth. There are also factors that impact DC/FC operations such as market wages, labor availability, process flow and customer requirements. To maintain a competitive advantage, the best companies have made automation a goal for ongoing DC/FC improvement to meet overall business objectives. Designing an effective profit producing supply chain is an ongoing process that needs to change with the times; businesses today should consider the benefits robots provide to the supply chain operation.
While automated robotic pickers and sorters can increase efficiency in many distribution facilities, each application needs to be carefully considered and designed to work with the rest of the process flow and operations. A business must carefully evaluate the requirements of the robotic automation and the overall business requirements for each situation needs to be considered, including capital expense, operating savings, performance improvement and customer service enhancement.
Some of the largest DC/FC operators in the U.S. have plans to automate almost every physical move in their facilities within the next two to three years. Robotic automation can extend the capacity, hours of operation, and life of a DC/FC. Robots are more affordable than ever and increasing wages and lack of available workers makes the economics more attractive and justifiable than in the past.
The future of the warehouse is happening now with robotics. Take a closer look at your operations to determine if robotic technology could be right for you.
Source: Material Handling & Logistics